Keep Your Line Running Smoothly with Reliable Packaging Machine Repair
Keep Your Line Running Smoothly with Reliable Packaging Machine Repair
Blog Article
Quick and Reliable Packaging Device Repair Work Services to Lessen Downtime
In the affordable landscape of production, the effectiveness of packaging operations rests on the dependability of equipment. Quick and trusted fixing services are essential in mitigating downtime, which can lead to considerable monetary losses and functional problems. Understanding the relevance of timely treatments and the function of professional service technicians can transform how services approach repair and maintenance. Nonetheless, browsing the myriad alternatives offered for fixing services can be difficult. What aspects should services consider to ensure they are making the ideal option for their operational requirements?
Significance of Timely Repair Works
Timely repair services of product packaging makers are critical for keeping operational effectiveness and lessening downtime. In the fast-paced setting of production and packaging, even minor malfunctions can lead to considerable hold-ups and performance losses. Attending to concerns without delay makes sure that makers run at their optimal ability, thereby securing the flow of operations.
In addition, routine and prompt maintenance can protect against the rise of minor problems right into significant break downs, which usually sustain greater fixing prices and longer downtimes. A positive approach to device repair work not just maintains the honesty of the devices yet additionally enhances the general integrity of the assembly line.
Additionally, timely repair services add to the durability of packaging machinery. Devices that are serviced immediately are less most likely to experience from extreme damage, enabling services to optimize their investments. This is specifically important in markets where high-speed product packaging is essential, as the need for constant performance is extremely important.
Benefits of Reliable Service Carriers
Reputable service suppliers play a pivotal role in guaranteeing the smooth operation of packaging machines. Their proficiency not only enhances the performance of repair services however additionally contributes dramatically to the long life of tools. Dependable service companies are geared up with the technical knowledge and experience essential to identify problems properly and implement efficient services swiftly. This reduces the threat of recurring troubles and makes certain that makers run at ideal performance degrees.
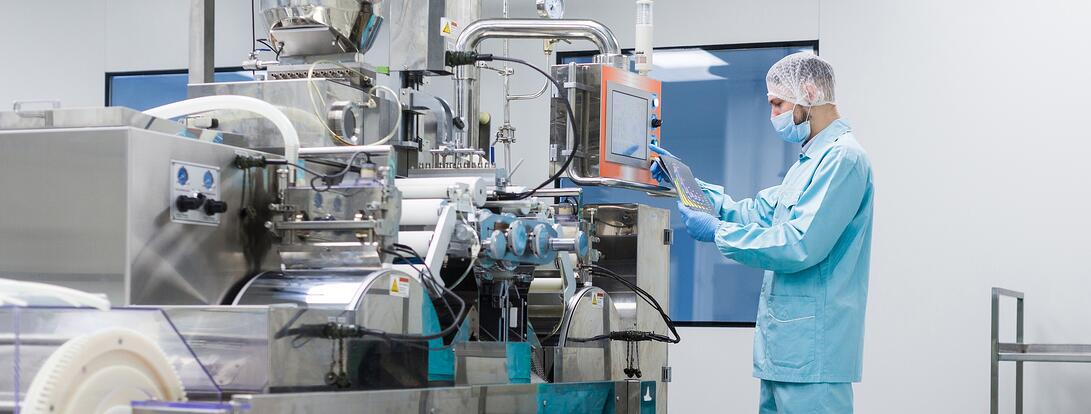
Furthermore, a reputable service copyright supplies comprehensive assistance, including training and guidance for personnel on device operation and upkeep finest methods. This not just equips staff members however likewise cultivates a society of safety and security and efficiency within the organization. Generally, the advantages of involving reputable provider extend beyond prompt fixings, positively impacting the whole functional process of product packaging processes.
Typical Product Packaging Equipment Issues
In the realm of product packaging procedures, different concerns can compromise the performance and performance of makers (packaging machine repair). Another typical concern is misalignment, which can create jams and uneven packaging, influencing product high quality and great site throughput.
Electrical issues can likewise interrupt product packaging operations. Faulty circuitry or malfunctioning sensors might lead to irregular maker behavior, creating hold-ups and increased functional costs. Additionally, software application glitches can prevent the equipment's programming, leading to operational inefficiencies.
Irregular item flow is another essential problem. This look here can occur from variations in product dimension, shape, or weight, which may impact the maker's capability to take care of items properly. Ultimately, insufficient training of operators can aggravate these issues, as inexperienced employees might not identify early indicators of malfunction or might misuse the equipment.
Attending to these common packaging equipment problems immediately is important to preserving productivity and ensuring a smooth operation. Routine evaluations and positive upkeep can considerably reduce these worries, fostering a trustworthy packaging atmosphere.
Tips for Lessening Downtime
To lessen downtime in product packaging operations, executing a proactive maintenance approach is essential. On a regular basis arranged maintenance checks can determine possible problems prior to they rise, guaranteeing devices run effectively. Establishing a routine that includes lubrication, calibration, and examination of critical components can substantially decrease the regularity of unforeseen breakdowns.
Training staff to run machinery appropriately and acknowledge early warning signs of breakdown can likewise play an essential duty. Empowering operators with the expertise to execute fundamental troubleshooting can avoid minor concerns from triggering major delays. Keeping an efficient inventory of important extra parts can expedite repair services, as waiting for parts can lead to extensive downtime.
Additionally, documenting equipment efficiency and upkeep activities can assist recognize patterns and recurrent problems, enabling targeted treatments. Integrating advanced tracking innovations can offer real-time information, allowing predictive maintenance and decreasing the risk of unexpected failures.
Last but not least, fostering open interaction between operators and upkeep teams ensures that any kind of abnormalities are promptly reported and addressed. By taking these proactive actions, services can boost functional performance and dramatically minimize downtime in product packaging procedures.
Choosing the Right Repair Work Service
Selecting the suitable fixing solution for packaging devices is an important decision that can substantially influence operational performance. A well-chosen solution copyright guarantees that your equipment is fixed promptly, properly, and to the greatest criteria. Begin by examining the company's experience with your certain sort of packaging tools. A professional acquainted with your equipment can identify concerns a lot more properly and apply services extra swiftly.
Next, think about the provider's online reputation. Seeking responses from various other businesses within your industry can offer insights right into dependability and high quality. Qualifications and partnerships with acknowledged tools suppliers can additionally suggest a dedication to quality.
Additionally, examine their reaction time and schedule. A company that can offer punctual support minimizes downtime and maintains manufacturing flow constant. It's also vital to make inquiries about service warranty and solution warranties, which can show the confidence the company has in their work.
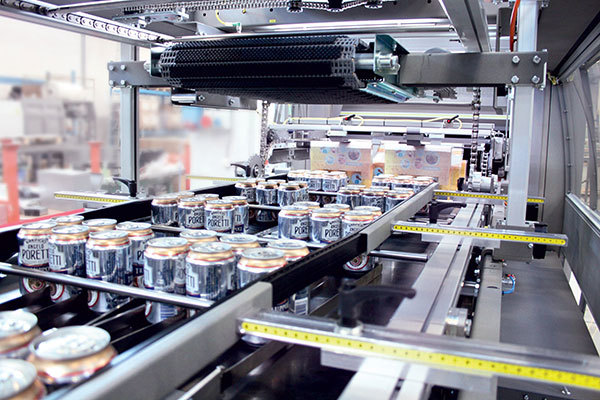
Conclusion
Finally, the relevance of fast and dependable packaging equipment fixing solutions can not be overstated, as they play an important role in decreasing downtime and guaranteeing functional efficiency. By focusing on timely repair work and selecting reliable company, organizations can properly keep and attend to typical concerns performance. Implementing positive maintenance practices and buying staff training further enhances the long life of packaging equipment. Inevitably, a critical technique to fix services cultivates a much more resistant manufacturing setting.
Timely repairs of product packaging makers are critical for maintaining operational Read More Here efficiency and decreasing downtime.Additionally, timely repair services add to the durability of product packaging equipment. On the whole, the advantages of engaging dependable solution providers expand past prompt repairs, positively affecting the entire operational workflow of packaging processes.

Report this page